¿Cómo lograr compensación y eficiencia energética incorporando tecnología?
- 18 de junio de 2021
- Posted by: Smart Clarity
- Categoría: Noticias
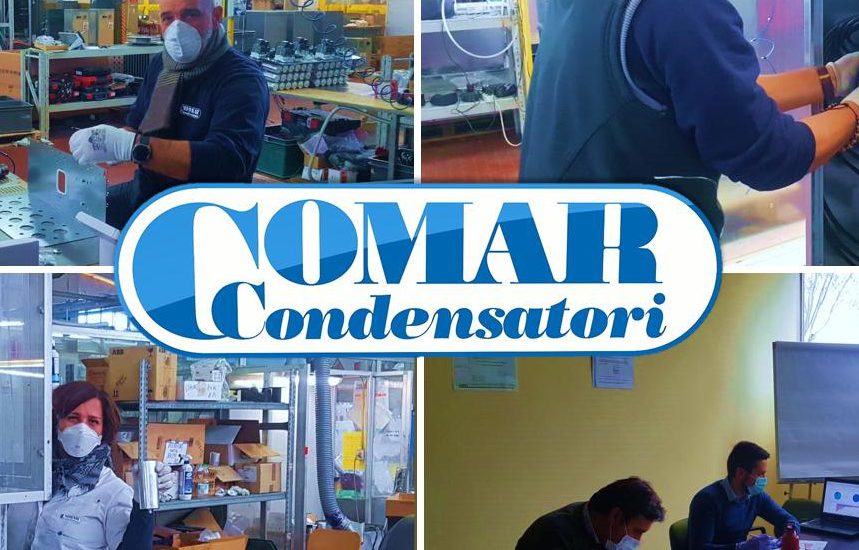
Uno de los caminos para generar eficiencia energética y considerada como una herramienta de eficiencia que impacte los recursos de las empresas, es incorporar equipamiento y tecnología. Primero hablaremos de un elemento fundamental en temas de mejoramiento energético: la compensación del factor de potencia. Y, segundo, la incorporación de la gestión, control y monitoreo de los sistemas energéticos.
La finalidad de la instalación de equipos de compensación de bancos de condensadores para corregir el factor de potencia, es mejorar la eficiencia del uso de la energía. Es pues la energía la que mueve todo y especialmente las industrias productivas se han comprometido con la competitividad y productividad. Hoy por hoy, la globalización ha permitido que en nuestra región cada vez se tenga mayor acceso a equipamientos que favorezcan la calidad de los productos, pero que además permitan competir con industrias a nivel mundial.
En nuestra región, contamos con compañías que están mejorando el factor de potencia, reduciendo las perdidas en energía reactiva y también los armónicos generados por el “switcheo” de los bancos de condensadores convencionales.
RESUMEN DE UN CASO DE ÉXITO CON LA INSTALACIÓN DE EQUIPOS DE COMPENSACIÓN COMAR:
Para la realización de este análisis se instalaron previamente equipos de medición y calidad y calidad de energía, luego se exportaron desde el software de medición de energía un mes y medio antes para tomar la situación y se midió un mes después con la respectiva calibración y ajuste.
La misión principal que tiene la instalación de un banco de condensadores es mejorar el factor de potencia. Esto trae muy buenos beneficios, pero nuestros equipos COMAR y la ingeniería en detalle que se realiza, para su cálculo y calibración, los hacen ir más allá de los simples efectos de mitigación y eliminación de multas. Este equipamiento al ser automático-electrónico, con reducción de armónicos y tristorizados, los hace ser equipos de ultima generación.
-
Factor de potencia.
El objetivo principal de la instalación de los bancos de condensadores es mejorar el factor de potencia. El resultado es que pasamos de tener un factor de potencia de 1.85 y luego de la instalación pasamos a mínimo 0.94 con un promedio de 0,97 y un máximo de 0,99. Disminuyendo la brecha entre el máximo y el mínimo del FP. Esto indica, que la estabilidad, eficacia con la operación del banco de condensadores, no solo eliminó las multas cuando eventualmente se presentaban, sino que controló la compensación inductiva y capacitiva debido a su conmutación electrónica en la etapa de potencia.
-
FECHA
Promedio de coseno Min
Promedio de coseno de fi Max
Promedio de coseno de fi Avg
Mes prev. 1
0,89
0,96
0,94
Mes prev. 2
0,88
0,95
0,94
Mes de intsalación
0,91
0,98
0,97
Pes post instalación
0,94
0,99
0,98
En este sentido el Factor de Potencia mejoró y se obtuvo una disminución en pérdidas en 118 kVAr (promedio) lo que equivale a una mejora del 36%. Y en cuanto a la potencia aparente sin entrar en detalles de sumas de cuadrados, se logró tener una diferencia menor igual a un 50%. esto muestra una mejora en la eficiencia en el uso de la energía.
Potencia Instantánea Promedio.
-
Columna1
Potencia Activa kW
Potencia Reactiva kVAr
Potencia Aparente kVA
Porcentaje diferencia
Mes prev 1
849,2
327,6
927,3
8%
Mes prev 2
818,8
323,5
898,8
9%
Mes instalación
719,2
199,6
763,1
6%
Mes post instalación
942,6
214,2
979,1
4%
De esta misma manera la diferencia de utilización con base entre kW y los kVAr muestra una mejora del 15% de la utilización de la energía Activa kW. Como resultado: un disminución en pérdidas de potencia en el sistema.
Potencia instantánea promedio 2.
-
Mes
Potencia Activa kW
Potencia Reactiva kVAr
Diferencia Activa Reactiva Porcentaje Utilizacion
Mes prev 1
849,2
327,6
521,6
61%
Mes prev 2
818,8
323,5
495,3
60%
Mes instalación
719,2
199,6
519,6
72%
Mes post instalación
942,6
214,2
728,3
77%
Para esta variable tenemos un THD de voltaje y corriente del sistema, donde vemos que se registra una disminución en el THD en magnitud y porcentaje del voltaje, valores que vemos a continuación:
-
Mes
Promedio de Tensión efectiva
Promedio de % THD Voltaje
Promedio de THD Voltaje L1
Mes prev 1
258,39
4,20%
7,16
Mes prev 2
261,07
2,70%
6,94
Mes instalación
260,64
3,10%
5,57
Mes post instalación
261,64
2,40%
6,25
Asimismo, se evidencia disminución en el THD en magnitud y porcentaje de la corriente, valores que se muestran en el cuadro:
-
Mes
Promedio de Corriente efectiva
Promedio de THD Corriente
Promedio de % THD Corriente
Mes prev 1
1129,36
192,81
19,00%
Mes prev 2
1103,29
208,57
19,50%
Mes instalación
926,25
168,07
19,70%
Mes post instalación
1240,29
170,81
14,30%
Una mínima disminución de armónicos en voltaje y corriente mejoró notablemente la calidad de la energía. Esto impacta en los costos de mantenimiento, daños de tarjetas electrónicas y demás variables asociadas a la calidad del producto.
Energía.
Diagrama de Pareto.
Para realizar el análisis del consumo de la energía, vamos a iniciar determinando el área de consumo de energía más alto para este centro productivo. La herramienta a utilizar es el diagrama de Pareto.
-
CENTRO DE COSTOS
CONSUMO ENERGIA
CONSUMO TOTAL
PORCENTAJE
PORCENTAJE ACUMULADO
PROCESO 1 C
699398,03
1567167,61
45%
45%
PROCESO 2 M
390314,00
1567167,61
25%
70%
PROCESO 3 S
355808,00
1567167,61
23%
92%
PROCESO 4 E
112388,03
1567167,61
7%
99%
PROCESO 5 E
9259,55
1567167,61
1%
100%
El Pareto se encuentra repartido entre los procesos 1, 2 y 3, ya que 2 y 3 son muy cercanos en proporción general.
Energía Vs Producción
En este caso, de acuerdo a los hallazgos, encontramos que hay una variación simultánea del consumo de la energía eléctrica con respecto a las toneladas producidas en el tiempo evaluado. Identificamos variaciones y relaciones diversas vs las toneladas producidas, ya que algunas son directamente proporcionales energía y producción y otras donde ni siquiera se produce y el consumo se mantiene, lo cual puede indicar que hay otras variables no medidas. En este análisis, hay un proceso que presenta un consumo fijo superior a 3900 Kwh día y muy poca relación con las toneladas producidas. Esto quiere decir que se tienen días con una producción similar, pero consumos de energía altos y bajos. Hay otros dos procesos que muestran comportamientos similares con el común denominador de relevante producción “0” con consumo en energía.
KW por Tonelada.
Al analizar los datos promedio de consumo en kW por tonelada, vemos una disminución del consumo de energía con respeto a los meses previos a la instalación de los bancos de condensadores, lo que indica un ahorro en energía eléctrica consumida.
kW por tonelada promedio mes
Etiquetas de fila |
Promedio de Kw/Tn proceso |
Promedio de w/Tn |
Promedio de Kw/Tn proceso |
Mes prev 1 |
7,33 |
7,96 |
15,26 |
Mes prev 2 |
9,89 |
10,39 |
17,25 |
Mes instalación |
8,55 |
9,29 |
17,44 |
Mes post instalación |
7,28 |
7,16 |
17,72 |
Consideraciones generales
-
Los bancos de condensadores COMAR instalados en una planta, muestran un comportamiento eficiente y una regulación muy precisa. Se nota el cambio desde su puesta en marcha con poca variación en el Factor de Potencia.
-
El consumo de energía Reactiva se redujo en un 36%, lo cual quiere decir que a pesar de reducir considerablemente este valor, no se elimina por completo, esta situación se puede haber presentado o es asociado a los kVar de los pasos de los condensadores.
-
Es evidente una mejora significativa en todas las variables de calidad de energía posterior a la instalación de los bancos de condensadores.
-
De acuerdo a la norma IEE519 para THD (Voltaje) sugiere el 5% para sistemas generales y THD (Corriente) 8% para límites entre Ic 20<50, se cumple a cabalidad en voltaje, y en corriente está en el límite superior, lo que nos hace pensar que debe mantenerse una visión de gestión, control y monitoreo para cumplir con las expectativas de mejora continua.
-
Implementar un SGEn debe ser la siguiente fase. Para ello, Smartclarity ha desarrollado, implementado y puesto en marcha una poderosa herramienta IoT (Clarity Energy) con el fin de optimizar, predecir, prevenir y mantener los parámetros deseados y cumplir con las normas técnicas.
-
Al encontrar procesos de mayor consumo y menor correlación con la producción, debemos verlo como una oportunidad de estudio y para ellos es indispensable, que esta revisión energética se mantenga de tal manera que se pueda obtener mayor impacto en el ahorro de energía consumida.
-
Este equipamiento, en este caso y en la mayoría de los casos que hemos tenido la oportunidad de intervenir, ha permitido desinstalar los equipos antiguos y usarlos en otras áreas de menor necesidad de control y manejo automático. Por esta razón, estas inversiones son recuperables en corto tiempo y no generan gastos adicionales en el futuro.
Fuente: Smartclarity